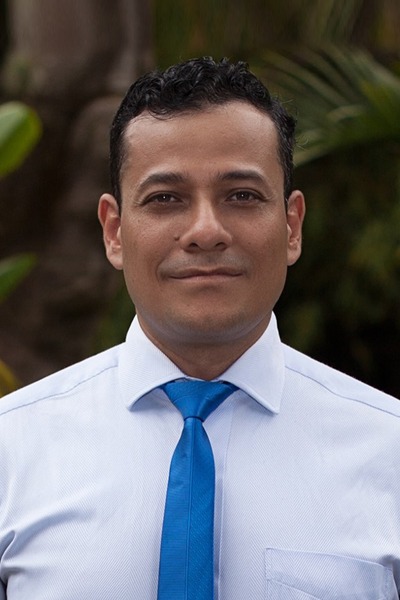
Optómetra ULS, Magíster Ciencias de la Visión. ULS. Especialista en Segmento Anterior y Lentes de Contacto USTA, FELLOW IACLE. Profesor Universidad De La Salle.
En la actualidad, los lentes de contacto requieren un mayor uso y desarrollo tecnológico debido a las necesidades visuales de los pacientes, principalmente causadas por irregularidades en la superficie corneal. Para lograr un correcto posicionamiento del lente, se requiere un cuidadoso diseño que considere aspectos como la curvatura de la superficie anterior y posterior, el diámetro, el corte y la forma de los bordes, así como parámetros funcionales como la zona óptica, las curvas periféricas, etc.
Las técnicas convencionales de fabricación de lentes de contacto incluyen el centrifugado, el moldeado y el torneado. En las dos primeras se utilizan polímeros líquidos que forman un lente ya sea por unión de dos moldes de curvas (moldeado) o por velocidad de centrifugado. Aunque estos métodos permiten la fabricación en masa, la adherencia del material al molde puede afectar en cierta medida la reproducibilidad. Para el caso del torneado, se utiliza un botón rígido de material que se corta en pasos para formar cada superficie, mediante el uso de una punta de diamante. La capacidad de generar curvas complejas dependerá de la tecnología del torno. Tal es el caso de los tornos numéricos, capaces de generar diferentes curvas especializadas entre las que se encuentran las asféricas, tóricas, multifocales, multicurvas, etc. A lo anterior se suma la capacidad de manejar materiales para cada método de fabricación y su costo de producción, lo cual influye en el acceso a los lentes.1
La demanda de métodos de fabricación más especializados para la generación de superficies más complejas se vuelve cada vez más relevante en el desarrollo de procesos dirigidos a la creación de lentes tipo Smart, cuyo objetivo adicional se traduce en la creación de dispositivos destinados al monitoreo de condiciones de salud como ojo seco, medición de la presión intraocular o la estimación del grado de glucosa en la superficie de contacto. En este sentido, la investigación requiere procesos de fabricación de lentes de contacto más avanzados, que incluyan el diseño, selección y fabricación del lente. Esto implica el uso de mejores materiales, una manufactura que garantice la estabilidad dimensional del dispositivo y un enfoque en aumentar la seguridad del paciente en lo que se refiere a la visión, salud de la superficie ocular y comodidad.1
Como alternativa de fabricación avanzada de lentes de contacto, la investigación ha recurrido a la tecnología aditiva, la cual ha revolucionado la industria en múltiples campos. Esta forma avanzada de fabricación consiste en la construcción de un modelo físico tridimensional (3D) a partir de un modelo diseñado digitalmente. Se trata de una manufactura asistida por computador. Su importancia en el ámbito de la salud radica en su capacidad para fabricar diferentes prototipos de dispositivos médicos. Cabe destacar que los productos obtenidos mediante esta tecnología aditiva ofrecen una precisión y reproducibilidad impresionantes. A todo este proceso se le conoce también como impresión en 3D.1
l proceso, que permite la fabricación de múltiples cantidades de algunos productos en menos tiempo, lo que incrementa la productividad. El avance tecnológico también ha incorporado materiales, flexibilidad en los procesos y en los diseños para imprimir en 3D.1
Considerando lo mencionado, la tecnología aditiva posee un gran potencial para la fabricación de lentes de contacto, especialmente en diseños personalizados que se adapten a cada caso específico. En este sentido, la fabricación en masa puede restar importancia al objetivo principal de lograr la impresión en 3D de un lente de contacto.
Existen diferentes técnicas de impresión 3D disponibles para la fabricación de lentes de contacto. Estas son: sinterizado selectivo por láser, modelado por deposición fundida, impresión estereoscópica de fotocurado con máquina de estereolitografía y procesamiento digital de luz. De los anteriores procesos, la estereolitografía (SLA, por su sigla en inglés) y el procesamiento digital de luz (DLP, por su sigla en inglés) han mostrado ser las preferidas en la investigación de impresión 3D para lentes de contacto.1
La razón por la cual ganan terreno las técnicas SLA y DLP se debe a la alta resolución y calidad de sus productos, que pueden estar formados por capas muy finas. Alam y colaboradores (2021), realizaron experimentos de fabricación de lentes de contacto mediante la técnica DLP usando una resina transparente. Los parámetros de impresión se diseñaron con el objetivo de optimizar el rendimiento de las superficies, garantizar una transmitancia adecuada y, adicionalmente, mantener las propiedades mecánicas estables.
Los resultados del experimento mostraron que el material usado, un monómero comúnmente usado, no se distorsionó durante el proceso de impresión, logrando una transmitancia luminosa del 90 %. Las características del material terminado en cuanto al módulo de tensión de Young y módulo de flexibilidad permitieron una estabilidad dimensional y manipulación adecuadas.1 Ver Figura 1.
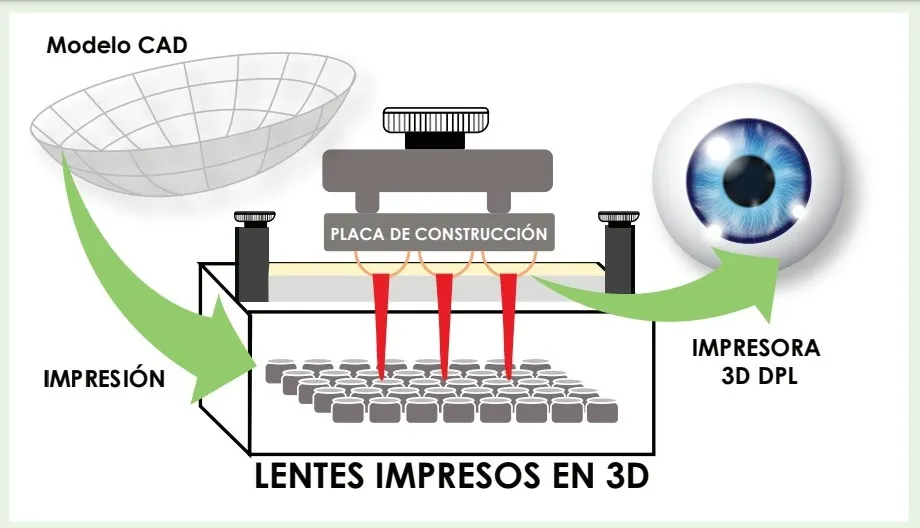
Continuando con la experimentación, se programó la impresora 3D para fabricar microcanales entre las capas cercanas a los bordes, con el potencial de incluir microsensores de nanotecnología para el estudio y monitoreo de condiciones vitales. Este proceso también fue exitoso y se lograron fabricar lentes estables. Como parte del modelo experimental, se incluyó la impresión de tinte en el lente, demostrando que el color no afecta la transmisión de luz y podría ser utilizado en el tratamiento de alteraciones de la visión cromática. Todo lo anterior muestra un camino prometedor para el futuro de la fabricación de lentes de contacto. La tecnología aditiva, por tanto, apoyará el proceso de adaptación personalizada de lentes de contacto con diseños únicos.1
Adaptado de:
- Alam F, Elsherif M, Alqattan B, Salih A, Lee SM, Yetisen AK, et al. 3D Printed Contact Lenses. ACS Biomater Sci Eng. 2021 Feb 8;7(2):794–803.